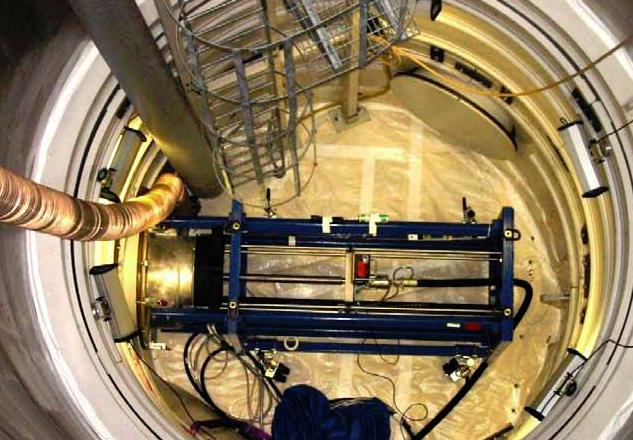
NuVision Engineering has over 40 years’ experience in nuclear energy generation and waste cleanup, is familiar with problems that arise in this sensitive field, and develops solutions to fix them.
The United States produces nearly 20 percent of its energy from nuclear power plants and has 104 of them, mostly dating back to the 1970s and beyond. Although America produces more nuclear electricity than any other nation, three-quarters of power stations are located abroad. China has 11 plants and a major program of construction; France generates 80 percent of its electricity needs from nuclear. This is a truly global industry.
Nuclear plants have to be not only robustly designed but also robustly maintained. NuVision Engineering was formed in 1971 asAEA Technology Engineering Services, Inc., and over the years it has delivered leading-edge technology solutions to a variety of customers including the US federal government, public utilities, international governments and a variety of domestic and international clients. In September 2006AEA (with offices in Pittsburgh; Mooresville, North Carolina; Sterling, Virginia; and Oak Ridge, Tennessee) was acquired by London-based Vision Capital and renamed NuVision Engineering.
NuVision Engineering’s core business is to develop and deliver techniques for use at commercial nuclear power plants and or hazardous and radioactive waste retrieval and treatment. The work falls into three main segments: commercial nuclear power, government waste remediation, and the fabrication and delivery of systems. The fabrication capability was added in 2009 when NuVision acquired Mid Columbia Engineering, Inc. (MCE) of Richland, Washington, a company that over the years has diversified into an extensive range of products and services including engineering, design, fabrication, commissioning and technical staffing supporting the nuclear and other industries.
The commercial nuclear work falls into three segments, the first being new plant and qualifications. Within the plants that are being constructed around the world NuVision is contracted to do mechanical, civil, structure design and engineering and component analysis needed to qualify components for manufacturing and installation.
The next segment focuses on operating plants, again involving a lot of engineering design and analysis. When a customer’s system fails they need to figure out why, so they contract with NuVision for that kind of work.
The third segment is the proprietary field services that NuVision provides for the plants. Perhaps the biggest single problem that has faced the nuclear power industry over the last 30 years has been the degeneration of a material known as Alloy 600. When a pipe, reactor vessel head nozzle or steam generation tube is welded, industry standards demand that the weld is tested to ensure that it is sound at the time. However, as the plants operate many of these Alloy 600 locations start to crack.
NuVision developed and patented a process called MSIP (Mechanical Stress Improvement Process) as a crack mitigation solution that overcomes this intractable problem of stress corrosion cracking in welds. Since that time MSIP has been applied at almost every nuclear plant in the US and a great number overseas. MSIP has been applied to over 6,000 welds around the world. The process eliminates the possibility of stress corrosion cracking in welds. The best time to utilize MSIP is before a crack appears, although it can be applied successfully as long as the crack is under 30 percent of the pipe thickness.
When steam generators are replaced, protecting workers from radiation exposure and minimizing the length of the outage are twin drivers. The connecting pipes become highly radioactive, so when the steam generator is cut out, the pipes need to be decontaminated. NuVision has a proprietary technology called Sponge Abrasive Decontamination to reduce radiation levels, so that when they put in a new steam generator, the welders can work without respirators.
While the NRC oversees the commercial nuclear industry, government nuclear plants and nuclear weapons facilities have their own problems, frequently associated with old tanks that start to leak radioactive material into the ground. NuVision has proprietary technologies that are very effective at cleaning up those wastes. Power fluidics is a skid-mounted vortex amplifier system that slurries and removes the radioactive sludge for safe long-term storage. The unique thing about power fluidics is that the sludge never touches a moving part, so nothing in the system is contaminated.
The challenges NuVision Engineering faces are safety in aging nuclear plants, plant modernization and improvement, and new plant optimization. Its solutions assess current condition, extend plant life, facilitate repairs, and validate and qualify the process. With more nuclear plants in the US a likelihood and global investment a certainty, the company is set to capitalize on its persistence in staying with its customers through a couple of decades when the nuclear industry contracted and competitors exited the business.